Bonded Abrasives: A Guide to Precision Machining & Finishing
This guide explores the crucial role of bonded abrasives in precision machining and finishing. Learn about material selection, grinding wheel codes, and optimizing your grinding process for superior results.
Anup Kumar
11/28/20242 min read
Precision Machining & Finishing: Achieving Excellence with Bonded Abrasives
In manufacturing, precision is paramount. Achieving tight tolerances and superior surface finishes requires the right tools and expertise. This guide explores the crucial role of bonded abrasives in precision machining and finishing, covering everything from material selection to optimizing grinding processes.
What are Abrasives?
Abrasives are materials with tiny, sharp cutting edges called grains. These grains remove material from a workpiece through cutting, scratching, and chipping actions. In manufacturing, bonded abrasives—where abrasive grains are held together in a rigid form—are essential for efficient material removal, shaping, and achieving dimensional accuracy.
Grinding Wheels: A Powerful Abrasive Tool
Grinding wheels are a common type of bonded abrasive, ideal for heavy-duty applications. They come in various shapes and sizes, designed for tasks like cutting, grinding, and finishing.
Choosing the Right Bonded Abrasive
Selecting the right bonded abrasive for your grinding process is crucial for achieving optimal results. Consider these factors:
Material Compatibility: Match the abrasive's hardness to the workpiece material. For example, aluminum oxide is often used for high-tensile strength materials like steel, while silicon carbide is better suited for materials with lower tensile strength.
Desired Finish: The desired surface roughness (Ra) will dictate the abrasive grit size. Coarse grits are used for rough shaping, while fine grits achieve smoother, more precise surfaces.
Bond Type: The bonding material affects the wheel's performance. Common options include vitrified, resinoid, rubber, and specialized bonds like ceramic or CBN for super-hard materials.
Understanding Grinding Wheel Codes
Grinding wheels have standardized codes that provide information about their composition. A typical code includes details about the abrasive type, grit size, grade, structure, and bond type. Learning to interpret these codes is crucial for making informed abrasive selections.
Optimizing Grinding Wheel Performance
To maximize grinding efficiency and achieve precision results:
Consider the application: Factor in the material being ground, the amount of stock to be removed, the contact area, and the grinding machine being used.
Control variables: Optimize wheel speed, work speed, machine condition, and operator skill level.
Specialized Grinding and Finishing Processes
Centerless Grinding: This process, used for cylindrical components, requires specialized abrasives and techniques to achieve precise diameters and roundness.
Honing, Lapping, and Superfinishing: These advanced finishing processes, often utilizing specialized bonded abrasives, can achieve even higher levels of precision and surface quality.
Innovations in Abrasive Technology
Continuous research and development in abrasive technology are leading to new bond materials and abrasive types that enhance performance, reduce costs, and meet increasingly demanding precision requirements.
The Bottom Line
Understanding bonded abrasives is crucial for efficient, cost-effective grinding and finishing processes. By making informed choices based on material compatibility, desired finish, and bond type, you can significantly improve productivity, reduce costs, and achieve superior product quality.
Need expert guidance on selecting the right abrasive solutions for your manufacturing needs? Contact AVB GLOBAL EXIM for personalized consulting and a wide range of high-quality bonded abrasives.
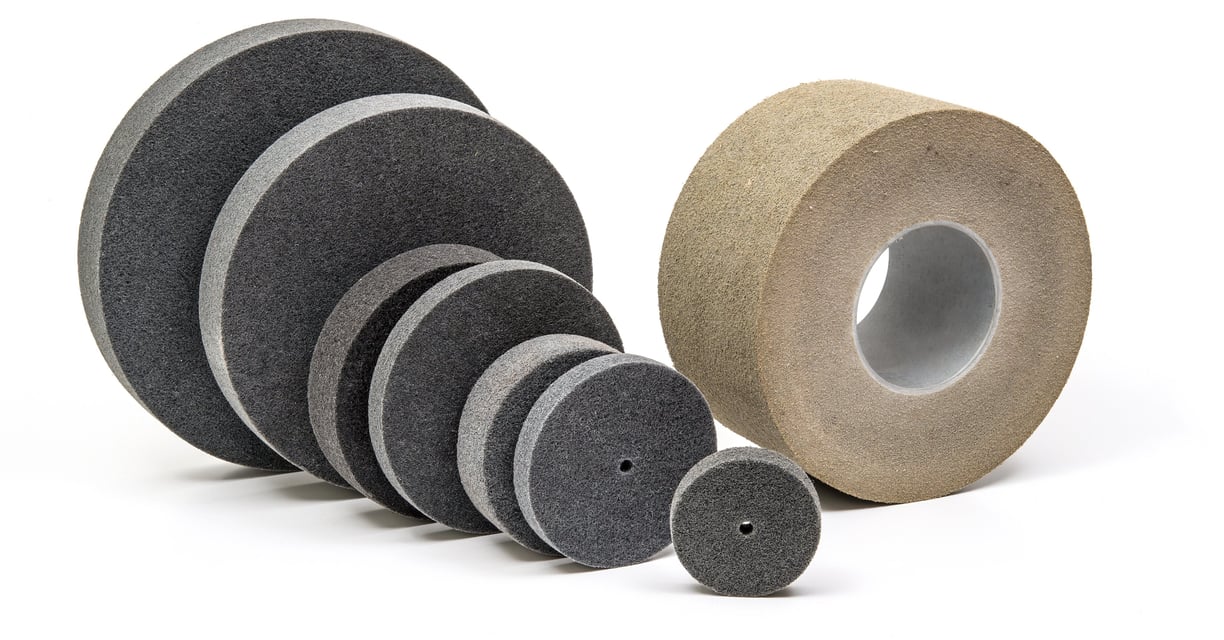
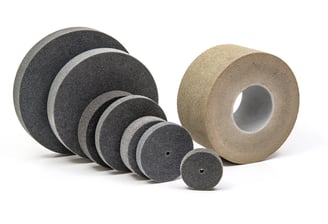


AVB GLOBAL EXIM is the registered trademark of AVB GLOBAL.© 2024 AVB GLOBAL EXIM.All Rights Reserved.
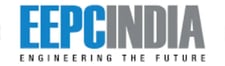
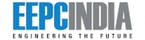
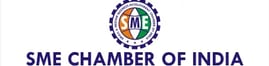
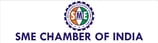